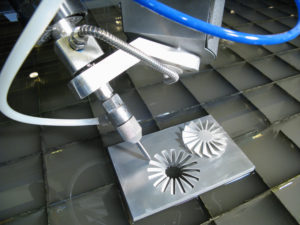
The Ultimate Guide to Maintaining Your Waterjet Machine
The Ultimate Guide to Maintaining Your Waterjet.
Waterjet cutting is one of the cleanest, most efficient methods to cut through a wide range of materials. Using a combination of high-pressure water and abrasive particles, waterjet cutters can slice through even the toughest materials, like steel, with unparalleled precision.
However, operating a waterjet cutter isn’t as simple as flipping a switch. These machines are part of intricate systems, requiring industrial power (up to 250 amps to start and 50 amps to maintain operation) and meticulous maintenance to ensure peak performance. Neglecting one component can lead to a ripple effect, impacting the entire system. To maximize the lifespan and efficiency of your waterjet, consistent maintenance and understanding its components are essential.
Here’s everything you need to know about maintaining your waterjet cutter effectively.
1. Stick to a Maintenance Schedule
The higher the operating pressure of your waterjet, the more often you’ll need to dedicate time to upkeep. Regular maintenance reduces unexpected breakdowns and ensures consistent cutting quality.
Start by developing a system to inspect and clean each part of the machine. Consult the manufacturer’s guidelines for replacement schedules and take advantage of available service plans. Additionally, many manufacturers and third-party providers offer training courses on waterjet maintenance. Whether you’re a novice or an expert, these courses can provide valuable insights to help you keep your machine in top shape.
2. Understand Your Waterjet’s Components
Your waterjet cutter is a collection of interdependent components—valves, seals, pumps, lines, and nozzles—all working together. If you source parts from multiple vendors, keeping track of everything can become complicated.
This is where partnering with a reliable supplier, like DTI, can make a difference. DTI offers personalized support, from system setup to project scheduling, and provides engineering expertise to help you understand your machine inside and out. Getting to know each part of your waterjet will not only help you troubleshoot problems faster but also empower you to perform preventive maintenance effectively.
3. Monitor Your Water Quality
Water quality plays a pivotal role in the longevity of your waterjet system. Hard water, laden with minerals, can drastically reduce the lifespan of components by causing buildup and inefficiencies.
Ensure your water has less than 100 parts per million (PPM) of total dissolved solids. If your water exceeds this threshold, invest in a treatment system—such as a water softener, reverse osmosis setup, or water recycling system—before installing your waterjet cutter. By addressing water quality early, you’ll save on repair costs and prolong the life of your machine.
4. Inspect the Cutting Head Regularly
The cutting head is the heart of your waterjet system, enabling precise, computer-controlled cuts. Signs of wear include cuts that are either too wide or too narrow, which often indicate nozzle clogging or misalignment.
Clogs can occur from excessive abrasive use, contamination, or accidental impacts with the cutting surface. Addressing these issues promptly can prevent further damage. Replacing a nozzle takes just 5 to 30 minutes, so don’t delay when you notice performance issues.
5. Clean the Mixing Chamber Daily
The mixing chamber is where the high-pressure water meets the abrasive, creating the cutting stream. Over time, natural wear and tear occur, and misalignment or debris buildup can shorten its lifespan.
Check the chamber daily to ensure its properly aligned and free of clogs. While most mixing chambers last around 500 hours, proactive maintenance can prevent premature replacements.
6. Protect the Orifice
The jewel inside the nozzle—made from rubies, sapphires, or diamonds—amplifies the water stream’s cutting power. Over time, the orifice diameter naturally expands when using ruby or sapphire, impacting cutting precision.
Rubies and sapphires last 40 to 80 hours, while diamonds can last up to 800 hours. Although diamonds cost more upfront, their longevity and reduced maintenance make them a cost-effective choice in the long run.
If you notice poor cut quality, check for potential issues like hard water buildup, worn high-pressure tubes, or faulty filters. Using an ultrasonic cleaner can help maintain the jewel’s condition and extend its lifespan.
7. Maintain the Water Flow Valve
The water flow valve regulates the water during the cutting process. A failing valve can result in leaks, wasted water, and inconsistent cutting performance.
Inspect the valve regularly to ensure no water drips when the machine is off. If replacement is necessary, the process typically takes 15 to 30 minutes and costs $100 to $200.
8. Replace Lines and Fittings When Needed
High-pressure lines and fittings have a typical lifespan of 2,000 hours but can wear out prematurely due to poor water quality, pressure spikes, or improper handling.
For a hassle-free replacement, consider pre-threaded high-pressure lines. While they’re slightly more expensive, they save time and effort during installation.
9. Don’t Overlook Small Components
Small parts like hand valves, elbows, and connectors play a crucial role in your waterjet system’s functionality. Regularly check these components for wear and tear.
Pay special attention to the filter located before the cutting head—it’s your last line of defense against hard water and debris. Depending on the design, filters can either be cleaned or replaced as needed.
10. Monitor High-Pressure Pumps
The high-pressure pump is the powerhouse of your waterjet. Key components—like seals, valves, cylinders, and plungers—must work in harmony to ensure proper performance.
Most waterjet systems include diagnostic software to monitor critical variables like oil, air, and water pressure. Take advantage of these tools to identify and address potential issues before they escalate.
Final Thoughts
Maintaining a waterjet cutter requires diligence, but the rewards are worth the effort. By following a consistent maintenance routine and addressing issues proactively, you’ll ensure your waterjet delivers optimal performance for years to come.
Whether you’re new to waterjet technology or a seasoned professional, ongoing training and support from experts can make a significant difference. Remember, your machine is always communicating—pay attention, and it will serve you well.
Share This Story, Choose Your Platform!